Appendix B — Division B
Fire Safety in High Buildings
B-3.2.6. Smoke Control for High Buildings
Experience with high buildings has shown that the time required for complete
evacuation can exceed that which is considered necessary for the safe egress of all
occupants. Studies of the “chimney effect” and observations of smoke movement in
actual fires have shown that fire compartmentation to contain a fire on any one
storey will not usually prevent the movement of smoke through elevator, stair and
other vertical shafts to the upper floors of a high building. Occupants of a high
building in which an automatic sprinkler system is not installed, and particularly
those on upper storeys, could be faced with severe smoke conditions from fires
occurring in storeys below them before their own evacuation is possible. The
requirements of Subsection 3.2.6. are intended to maintain safe
conditions for occupants of a high building who may have to remain in the building
during a fire, and to assist the firefighters by providing efficient access to the
fire floor. The material in this Appendix is intended to assist a designer in
complying with the requirements of Subsection 3.2.6. The
knowledge requirements are well within the capabilities of a competent designer. The
designer should appreciate, however, that successful application requires a clear
understanding of the principles that govern smoke movement. Subsection 3.2.6. contains only those items that relate to the design and
construction of a building; operation of the facilities and recommended actions to
be taken by the building owner, occupant and fire department are covered by the
British Columbia Fire Code.
The designer is cautioned that the tabular and graphical information in this
Appendix has been developed for buildings having conventional configurations. The
designer has to judge the extent to which the building under consideration has
characteristics that will allow the application of this information; this is
particularly true of designs employing air-handling systems for which a realistic
assessment of the leakage characteristics of the enclosures of spaces may be
critical.
It is assumed that buildings regulated by Subsection 3.2.6. will
be in an area served by a fire department capable of an early response and that all
firefighting and rescue situations will be under the direct control of the
officer-in-charge of the fire department responding to the emergency. It is
important that firefighters be provided with a smoke-free access to fire floors
below grade. Provisions are included to separate exit stairways serving storeys
above grade from those serving storeys below grade, and to limit entry of smoke into
these shafts. Similarly, elevator hoistways and service shafts are required to be
provided with a separation near grade, or be designed to limit their functioning as
paths of smoke movement into upper floor areas from storeys below grade.
It is assumed that in the event of fire, occupants of the floor on which the fire
occurs will leave by exit stairs immediately following the sounding of a fire alarm,
and that occupants of the floor immediately above the floor on which the fire occurs
will be advised to leave by the first fire department officer on the scene or other
person assigned this responsibility. Occupants of all other floors may remain on
their floors unless otherwise directed. It is also assumed that the owner of the
building has complied with the Emergency Planning Section of the British Columbia
Fire Code by preparing a comprehensive fire safety plan to safeguard the building
occupants and that the building supervisory staff are familiar with the requirements
of Subsection 3.2.6. and with their responsibilities under the fire safety
plan.
The British Columbia Building Code requires that a check be made of the smoke
control and mechanical venting systems. Testing will indicate deficiencies caused
by
inexact estimates of the leakage characteristics or of air supply requirements and,
in all but the most extreme cases, will provide an opportunity for appropriate
adjustments before the system is put into service.
B-3.2.6.2.(2) Stairway Protection Below Lowest Exit Level
A stairway serving floors below the lowest exit level is considered to comply with
the intent of Sentence 3.2.6.2.(2) if the following conditions are satisfied.
1) The stairway has a vent or door to the outdoors at or near the top of the
stairshaft that has an openable area of not less than 0.1
m2 for each storey served by the stairway, less 0.01
m2 for each weatherstripped door and 0.02
m2 for each door that is not weatherstripped opening
into the stairway.
2) The stairway is enclosed in a shaft that
- does not pass through the floor above the lowest exit level and is separate from a shaft that contains a stairway serving upper storeys, or
- contains a stairway serving upper storeys, but is separated from that stairway at the lowest exit level by a fire separation having a fire-resistance rating not less than that required for the shaft enclosure.
3) The stairway is provided with equipment capable of maintaining a flow of air
introduced at or near the bottom of the stair shaft, at a rate equal to 0.47
m3/s for each storey served by the
stairway.
B-3.2.6.2.(3) Pressurization of Stair Shafts
The purpose of providing open doors and vents at the bottom of a stair shaft is to
create a positive pressure in the shaft relative to adjacent floor areas and thus
keep it free of smoke. The pressure depends on the temperature differential between
the interior and the exterior of the building which is most pronounced during winter
months when stack effect is greatest. If a shaft does not have a direct opening to
the exterior, alternative means must be provided to achieve smoke control. If a
corridor or vestibule is used as a link between the exit level of an interior stair
shaft and the outdoors to provide a venting system, it will be necessary to assess
the reliability of the overall system. The probability of all doors or closures
being opened at the same time has to be addressed, as well as the size of the
vestibule and its impact on the overall smoke control system.
If mechanical methods are used to develop a positive pressure in a stair shaft, a
minimum pressure differential of 12 Pa is recommended to prevent smoke
migration from floor areas in a sprinklered building where fire temperatures are
controlled and smoke movement may be dominated by stack effect in a stair shaft.
During a fire emergency, persons will be entering and exiting a stair shaft as they
move to a place of safety and under these conditions the number of doors open to the
stair shaft cannot be predetermined. The number will vary depending on the occupancy
of the building, population density and the evacuation plan for the building. It
should be assumed that two doors are open. This is based in part as a practical
level for most buildings and considers the positive fire experience in sprinklered
buildings.
The maximum pressure differential created by a mechanical system should not
prevent doors to the stair shafts from being opened. A specific maximum value cannot
be given, as this value will depend on the door opening force and size of the door.
These values should be calculated for each specific case. Although a maximum value
of 130 N is suggested by research as the force that can be opened by
the majority of people in most occupancies, this value is above the maximum value
of
90 N generally specified in this Code. The use of values below
130 N can create a practical problem in achieving effective smoke
control as it is difficult to design for the acceptable minimum and maximum pressure
differential range. Special consideration may need to be given for doors located in
an accessible path of travel.
Care should be taken by designers and by building and fire officials in
implementation of these requirements. Assumptions involved in the design of a smoke
control system may be different from final construction conditions. For this reason
each system should be tested after installation to ensure that the design intent is
met. The minimum pressure differential is not intended to apply to locations in
stair shafts when doors in their proximity are open to adjacent floor areas.
B-3.2.6.2.(4) Limiting Smoke Movement
Measures to prevent the migration of smoke from floor areas below the lowest exit
storey into upper storeys include the following.
1) An elevator hoistway that passes through the floor above the lowest exit storey
should not penetrate the floor of the storey immediately below the lowest exit
storey, unless there is a vestibule between the shaft and each floor area below the
lowest exit storey that
- has a fire separation, with a fire-resistance rating not less than 45 min, between the vestibule and any public corridor,
- has a fire separation, with a fire-resistance rating not less than that required for an exit by Article 3.4.4.1., between the vestibule and any stair or elevator enclosure or any part of a floor area, other than a public corridor, and
- except for elevator hoistway entrances, has a self-closing device on any door through the fire separation required by Clauses (a) and (b), with the door opening in the direction of travel from the floor area to the exit stairway.
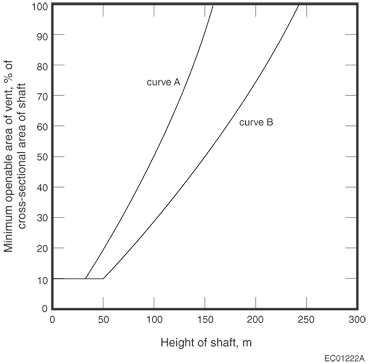
Figure B-3.2.6.2.(4)-A
Vent to a vertical service space with no other pressurized shaft in the
building
Notes to Figure B-3.2.6.2.(4)-A:
|
|
(1) |
Curve A applies to a vertical service space that is enclosed by
unplastered unit masonry or by plaster and steel stud construction with all
openings in the shaft sealed to the degree required by Articles 3.1.9.1. to 3.1.9.4. |
(2) |
Curve B applies to a vertical service space that is enclosed by
monolithic concrete or by plastered unit masonry with all openings in the shaft
sealed tightly to minimize air leakage.
|
(3) |
A shaft having a vent that is 100% of the cross-sectional area of the
shaft is acceptable for buildings up to 1.5 times the height shown by the
appropriate curve in Figures B-3.2.6.2.(4)-A and B-3.2.6.2.(4)-B.
|
(4) |
The total leakage area, based on measurements in typical high buildings,
is assumed to be 0.025 m2 for every 10
m2 of shaft wall area in the case of Curve A and
0.015 m2 for every 10
m2 of shaft wall area in the case of Curve
B.
|
2) A vertical service space, other than an elevator hoistway, that passes through the
floor assembly above the lowest exit storey, should be provided with a tight-fitting
noncombustible seal or fire stop at the floor assembly of the storey immediately
below the lowest exit storey, unless
- the vertical service space is vented to the
outdoors at the top and the vent has an openable area that is not less
than
- that obtained from Figure B-3.2.6.2.(4)-A if the vertical service space is in a building in which other shafts are not mechanically pressurized, or
- that obtained from Figure B-3.2.6.2.(4)-B if the vertical service space is in a building in which other shafts are mechanically pressurized,
- for a shaft that serves floor areas above
the lowest exit storey, a vent is located
- at or near the top of the shaft if the shaft is above the mid-height of the building, or
- at or near the foot of the shaft at or near the exit level if the top of the shaft is below the mid-height of the building, or
- for a shaft that serves floor areas below the lowest exit storey, a vent is located at or near the top of the shaft.
3) Any closure provided for a vent opening referred to in Sentence (2) must be openable:
- manually,
- on a signal from a smoke detector located at or near the top of the shaft, and
- by a control device located at the central alarm and control facility.
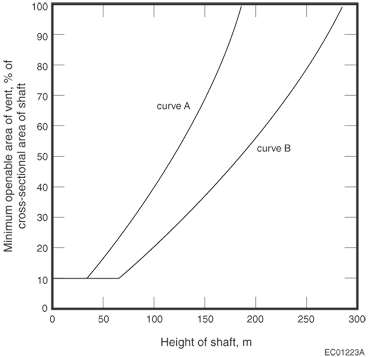
Figure B-3.2.6.2.(4)-B
Vent to a vertical service space with other pressurized shafts in the
building
Notes to Figure B-3.2.6.2.(4)-B:
|
|
(1) |
Curve A applies to a vertical service space that is enclosed by
unplastered unit masonry or by plaster and steel stud construction with all
openings in the shaft sealed to the degree required by Articles 3.1.9.1. to 3.1.9.4. |
(2) |
Curve B applies to a vertical service space that is enclosed by
monolithic concrete or by plastered unit masonry with all openings in the shaft
sealed tightly to minimize air leakage.
|
(3) |
A shaft having a vent that is 100% of the cross-sectional area of the
shaft is acceptable for buildings up to 1.5 times the height shown by the
appropriate curve in Figures B-3.2.6.2.(4)-A and B-3.2.6.2.(4)-B.
|
(4) |
The total leakage area, based on measurements in typical high buildings,
is assumed to be 0.025 m2 for every 10
m2 of shaft wall area in the case of Curve A and
0.015 m2 for every 10
m2 of shaft wall area in the case of Curve
B.
|
B-3.2.6.3.(1) Connected Buildings
The measures described here are intended to prevent movement of smoke from one
building to another. They are of particular significance for two buildings of
unequal height that are joined together. The techniques suggested are the provision
of a large opening to the outdoors in a connecting vestibule so that smoke entering
through leakage areas around doors will be vented to the outdoors, or pressurization
to maintain a higher pressure in the vestibule than in adjacent spaces, as
illustrated in Figures B-3.2.6.3.(1)-A, B-3.2.6.3.(1)-B and B-3.2.6.3.(1)-C.
The provisions for protection of openings are described in terms appropriate to a
doorway. Openings other than doorways should be avoided if possible. Openings should
be protected by an airlock that gives the same standard of protection as the
vestibule referred to below.
The requirement of Article 3.2.6.3. that limits movement of smoke from one building to another may be met by
incorporating in the link between the buildings the provisions of Sentences (1) and (2).
1) A firewall conforming to Subsection 3.1.10. is
constructed between one building and the other with any opening in the firewall
protected against the passage of smoke by a vestibule that has
- a fire separation between the vestibule and a public corridor with a fire-resistance rating not less than 45 min,
- a fire separation between the vestibule and the remainder of the floor area, other than a public corridor, with a fire-resistance rating not less than that required by Article 3.4.4.1. for an exit,
- a fire separation between the vestibule and a stair enclosure or elevator hoistway with a fire-resistance rating not less than that required by Article 3.4.4.1. for an exit, and
- any door in the fire separation required by Clauses (a), (b) or (c), except for an elevator entrance, provided with a self-closing device as required by Article 3.1.8.11. and opening in the direction of travel from the floor area to the exit stairway.
2) The vestibule referred to in Sentence (1) should have
- a vent to the outdoors that has a net area of 10(0.023 d + 0.00045 a) m2, where 'd' is the number of doors having a perimeter not more than 6 m that open into the vestibule, or if the perimeter of doors exceeds 6 m, the value 'd' is increased in direct proportion to the increase in the perimeter, and 'a' is the area in square metres of enclosing walls, floors and ceilings whose outer face is in contact with the outside air, except that where the outer face of a wall is in contact with the ground or fill, it is assumed that there is no leakage through that portion, and the value of 'a' is assumed to be zero, or
- equipment capable of maintaining a supply of air into the vestibule sufficient to ensure that the air pressure in the vestibule when the doors are closed is higher by at least 12 Pa than that in adjacent floor areas when the outdoor temperature is equal to the January design temperature on a 2.5% basis.
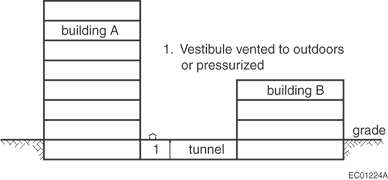
Figure B-3.2.6.3.(1)-A
Buildings connected by a tunnel
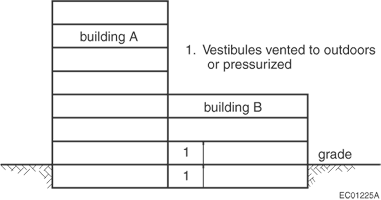
Figure B-3.2.6.3.(1)-B
Buildings connected at a firewall
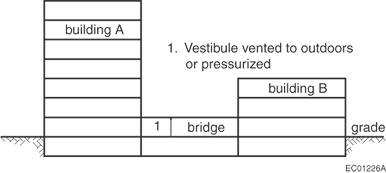
Figure B-3.2.6.3.(1)-C
Buildings connected by a bridge
B-3.2.6.5.(6)(b) Electrical Cable Protection
Electrical cables that provide continuous operation for 1 h when
subjected to the fire exposure of the time/temperature curve of CAN/ULC-S101, “Fire Endurance Tests of Building Construction and Materials,” do not need additional protection against exposure to fire.
B-3.2.6.6.(1) Venting to Aid Firefighting
The requirements of Sentence 3.2.6.6.(1) are met by incorporating in a floor area windows or wall panels, as described in Sentence (1), by smoke shafts as described in Sentences (2) to (8), or by the use of building exhaust systems as described in Sentence (9).
1) If windows or wall panels are used for venting, they must
- be uniformly distributed along the exterior wall of each storey,
- have a total area not less than 1% of the exterior wall area of each storey,
- be readily openable from the interior without the use of wrenches or keys,
- be readily identified from the interior, and from the exterior where they are accessible to firefighters, and
- be designed so that when opened they will not endanger persons outside the building during a fire.
2) If one or more smoke shafts or vertical service spaces are used for venting, they
must
- have an opening or openings into each storey with an aggregate area not less than that obtained from Table B-3.2.6.6.(1)A for the height of the building and the area of the largest floor area served by the smoke shaft, and the leakage characteristics of the shaft wall and closures obtained from Table B-3.2.6.6.(1)B, and Table B-3.2.6.6.(1)C,
- have an aggregate unobstructed cross-sectional area equal to that required by Clause (a), and
- be designed to comply with the requirements of Sentence (3).
3) Each smoke shaft or vertical service space described in Sentence (2) must
- be separated from the remainder of the building by a fire separation that has a fire-resistance rating not less than that required for the floor assembly through which it passes, or be designed as a chimney conforming to Part 6, except that flue liners need not be provided,
- have an opening to the outdoors at the top that has an area not less than the cross-sectional area of the shaft, with the opening protected from the weather,
- terminate not less than 900 mm above the roof surface where it penetrates the roof, and
- contain no combustible material, fuel lines or services that are required for use in an emergency.
4) Each opening required by Clause (2)(a) must be located so that the top of the
opening is not more than 250 mm below the ceiling, except that the
opening may be above the ceiling if the ceiling freely allows passage of
air.
5) The opening into the smoke shaft must be provided with a closure that
- has a fire-protection rating conforming to Sentence 3.1.8.4.(2), except that the temperature on the unexposed face of the closure shall be not more than 250 °C after 30 min during the fire test used to determine its rating,
- is no closer to combustible material, except for paint or tightly-adhering paper covering not more than 1 mm thick applied to a noncombustible backing, than the distances described in Table B-3.2.6.6.(1)D,
- can be opened from a remote location such as a stair shaft, the storey immediately below, or the central alarm and control facility, and
- does not open automatically on any floor, other than the fire floor, when smoke and hot gases pass through the shaft.
6) Closures for openings described in Clause (3)(b) must
- be openable from outside the shaft, and
- open automatically
- on a signal from a smoke detector in the shaft,
- by operation of the fire alarm system, and
- when the closure required by Sentence (5) opens.
7) A smoke shaft opening referred to in Sentence (2) that is less than 1 070 mm above the floor must conform to Article 3.3.1.18.
8) If a closure is required to comply with Sentence (5), the leakage area between closure components and between closure and frame must not be
more than 3% of the openable area of the closure.
9) The building air handling system may be used for smoke venting, provided
- the system can maintain an exhaust to the outdoors at the rate of 6 air changes per hour from any floor area, and
- emergency power to the fans providing the exhaust required by Clause (a) is provided as described in Article 3.2.7.9.
Table B-3.2.6.6.(1)A Minimum Size of Vent Openings into Smoke Shafts from Each Floor Area, m2(1)(2) Forming part of Appendix Note B-3.2.6.6.(1) | ||||||||||
Floor |
Leakage Area, %(3) | Building Height, m | ||||||||
18 | 37 | 73 | 110 | 146 | 183 | 220 | 256 | 293 | ||
200 | 0 | 0.10 | 0.11 | 0.13 | 0.15 | 0.16 | 0.18 | 0.19 | 0.20 | 0.22 |
500 | 0.22 | 0.25 | 0.29 | 0.32 | 0.36 | 0.37 | 0.39 | 0.41 | 0.43 | |
1 000 | 0.43 | 0.48 | 0.53 | 0.59 | 0.63 | 0.67 | 0.71 | 0.75 | 0.77 | |
2 000 | 0.83 | 0.91 | 1.01 | 1.08 | 1.16 | 1.22 | 1.29 | 1.34 | 1.39 | |
3 000 | 1.21 | 1.33 | 1.46 | 1.55 | 1.67 | 1.75 | 1.82 | 1.90 | 1.97 | |
4 000 | 1.62 | 1.75 | 1.90 | 2.02 | 2.15 | 2.25 | 2.35 | 2.44 | 2.53 | |
5 000 | 2.01 | 2.17 | 2.34 | 2.46 | 2.63 | 2.74 | 2.86 | 2.88 | 3.07 | |
6 000 | 2.39 | 2.57 | 2.76 | 2.91 | 3.10 | 3.23 | 3.37 | 3.47 | 3.58 | |
200 | 1 | 0.10 | 0.12 | 0.15 | 0.19 | 0.22 | 0.27 | 0.35 | 0.43 | 0.55 |
500 | 0.23 | 0.27 | 0.35 | 0.40 | 0.49 | 0.57 | 0.69 | 0.83 | 1.04 | |
1 000 | 0.44 | 0.50 | 0.71 | 0.72 | 0.86 | 1.01 | 1.19 | 1.43 | 1.73 | |
2 000 | 0.85 | 0.97 | 1.15 | 1.33 | 1.56 | 1.81 | 2.10 | 2.48 | 2.95 | |
3 000 | 1.26 | 1.42 | 1.67 | 1.91 | 2.23 | 2.56 | 2.97 | 3.47 | 4.08 | |
4 000 | 1.66 | 1.88 | 2.18 | 2.49 | 2.37 | 3.28 | 3.79 | 4.40 | 5.16 | |
5 000 | 2.07 | 2.32 | 2.69 | 3.05 | 3.51 | 3.99 | 4.60 | 5.32 | 6.21 | |
6 000 | 2.47 | 2.76 | 3.18 | 3.59 | 4.14 | 4.68 | 5.37 | 6.20 | 7.23 | |
200 | 2 | 0.10 | 0.13 | 0.18 | 0.24 | 0.37 | 0.61 | 1.28 | 4.60 | 89.57 |
500 | 0.24 | 0.29 | 0.39 | 0.52 | 0.75 | 1.13 | 2.10 | 6.11 | 94.50 | |
1 000 | 0.46 | 0.55 | 0.72 | 0.94 | 1.30 | 1.90 | 3.27 | 8.29 | 102.11 | |
2 000 | 0.88 | 1.05 | 1.34 | 1.73 | 2.32 | 3.28 | 5.36 | 12.14 | 116.80 | |
3 000 | 1.31 | 1.53 | 1.95 | 2.47 | 3.29 | 4.58 | 7.28 | 15.63 | 130.83 | |
4 000 | 1.73 | 2.01 | 2.55 | 3.20 | 4.23 | 5.83 | 9.12 | 19.97 | 144.03 | |
5 000 | 2.15 | 2.49 | 3.13 | 3.92 | 5.15 | 7.05 | 10.90 | 22.15 | 157.05 | |
6 000 | 2.57 | 2.96 | 3.73 | 4.63 | 6.07 | 8.26 | 12.65 | 25.39 | 169.29 | |
200 | 3 | 0.11 | 0.14 | 0.21 | 0.37 | 0.88 | 2.06 | |||
500 | 0.25 | 0.31 | 0.47 | 0.76 | 1.58 | 9.00 | ||||
1 000 | 0.47 | 0.59 | 0.86 | 1.33 | 2.60 | 11.99 | ||||
2 000 | 0.91 | 1.12 | 1.60 | 2.41 | 4.47 | 17.46 | ||||
3 000 | 1.35 | 1.64 | 2.31 | 3.43 | 5.21 | 22.48 | ||||
4 000 | 1.79 | 2.17 | 3.02 | 4.43 | 7.91 | 27.29 | ||||
5 000 | 2.22 | 2.68 | 3.71 | 5.42 | 9.55 | 31.95 | ||||
6 000 | 2.65 | 3.20 | 4.40 | 6.39 | 11.18 | 36.47 | ||||
200 | 4 | 0.11 | 0.15 | 0.28 | 0.70 | 24.83 | ||||
500 | 0.25 | 0.34 | 0.58 | 1.33 | 29.18 | |||||
1 000 | 0.49 | 0.63 | 1.06 | 2.27 | 36.07 | |||||
2 000 | 0.95 | 1.21 | 1.97 | 3.99 | 48.56 | |||||
3 000 | 1.41 | 1.78 | 2.84 | 6.63 | 60.15 | |||||
4 000 | 1.86 | 2.34 | 3.70 | 7.22 | 71.15 | |||||
5 000 | 2.21 | 2.90 | 4.55 | 8.79 | 81.81 | |||||
6 000 | 2.75 | 3.46 | 5.40 | 10.33 | 90.05 | |||||
200 | 5 | 0.11 | 0.16 | 0.36 | 3.33 | |||||
500 | 0.28 | 0.36 | 0.76 | 5.09 | ||||||
1 000 | 0.50 | 0.69 | 1.37 | 7.67 | ||||||
2 000 | 0.99 | 1.31 | 2.54 | 12.35 | ||||||
3 000 | 1.46 | 1.94 | 3.65 | 16.75 | ||||||
4 000 | 1.92 | 2.55 | 4.75 | 20.99 | ||||||
5 000 | 2.40 | 3.16 | 5.84 | 25.11 | ||||||
6 000 | 2.87 | 3.74 | 6.92 | 29.11 |
Notes to Table B-3.2.6.6.(1)A: | |
|
|
(1) | The minimum size of a vent opening into a smoke shaft is obtained from Table B-3.2.6.6.(1)A and is dependant on the floor area and total leakage area of the smoke shaft walls and closures. This total leakage area may be estimated by adding the leakage areas for the shaft wall obtained from Table B-3.2.6.6.(1)B and for the dampered openings obtained from Table B-3.2.6.6.(1)C, provided the cross-sectional area of the smoke shaft, the opening into the shaft and the opening to the outdoors at the top of the shaft are equal. |
(2) | The size of the vent opening refers to the free or unobstructed area of the opening. |
(3) | Leakage area is the total of the leakage area of smoke shaft wall obtained from Table B-3.2.6.6.(1)B and the leakage area of openings in smoke shafts obtained from Table B-3.2.6.6.(1)C. |
Table B-3.2.6.6.(1)B Leakage Area of Smoke Shaft Wall Forming part of Appendix Note B-3.2.6.6.(1) | |
Wall Construction | Leakage Area as % of Wall Area |
Monolithic concrete | 0.5 |
Masonry wall unplastered | 1.5 |
Masonry wall plastered | 0.5 |
Gypsum board on steel studs | 1.0 |
Table B-3.2.6.6.(1)C Leakage Area of Closures in Openings into Smoke Shaft Forming part of Appendix Note B-3.2.6.6.(1) | |
Type of Closure | |
Curtain fire damper | 2.5 |
Single-blade fire damper | 3.5 |
Multi-blade fire damper | 4.5 |
Notes to Table B-3.2.6.6.(1)C: | |
|
|
(1) | Values include allowance for 0.5% leakage between frame and wall construction. |
(2) | These leakage data are based on clearances applicable to closures that have been tested in accordance with CAN/ULC-S112-M, “Fire Test of Fire-Damper Assemblies.” |
Table B-3.2.6.6.(1)D Minimum Distance from Closure to Combustible Material Forming part of Appendix Note B-3.2.6.6.(1) | ||
Area of Closure(1), m2 | Minimum Distance in Front of or Above Closure, m | Minimum Distance to the Sides or Below Closure, m |
0.5 | 0.35 | 0.20 |
1.0 | 0.50 | 0.25 |
1.5 | 0.60 | 0.30 |
2.0 | 0.70 | 0.35 |
2.5(2) |
0.80 | 0.40 |
Notes to Table B-3.2.6.6.(1)D: | |
|
|
(1) | For closure areas between those given in Table B-3.2.6.6.(1)D, interpolation may be used to determine the appropriate distances. |
(2) | For closure areas greater than 2.5 m2, the minimum distance in front of or above the closure shall be one half of the square root of the closure area, and the minimum distance to the sides or below the closure shall be one quarter of the square root of the closure area. |
B-3.2.6.7.(1) Protection of Central Control Room
The design of a room provided for a central alarm
and control facility should take into account the nature and sensitivity
of the electronic components of the equipment and the room should
be adequately protected from fire and smoke. The room should be ventilated
with a supply of fresh air so that it has a clean environment and
should be provided with adequate lighting.
B-3.2.6.7.(2) Central Control Room Air Control
Depending on the method of mechanical venting and air control
that is selected for the building, additional controls may be required
at the central alarm and control facility. These additional controls
include those with a capability of opening closures to vents in shafts,
stopping air-handling systems, and initiating mechanical air supply
to stair shafts.
B-3.2.6.9.(1) Testing for Smoke Control
The efficiency of a smoke control system may be checked by
measuring pressure differences and the directions of airflow around
doors and through separating walls of compartments. A pressure meter
can be used to measure pressure differences on either side of a door
or partition. Where this is impracticable, a punk stick held near
a crack will indicate the direction of airflow. Measurements of airflow
may be taken on the intake side of supply fans or in supply ducts
to determine whether the specified airflow is being provided. In general,
airflow should be from the spaces which may be occupied for various
lengths of time during a fire emergency (e.g., vestibules, stair shafts,
and elevator hoistways) toward the space in which the fire is assumed
to have occurred. Measurements may be taken at certain critical locations
to check the overall efficiency of the smoke control system.
In buildings where protection is obtained by venting corridors
or vestibules to the outdoors, inspection of the building to determine
whether the requirements have been met should be sufficient. Where
service shafts are vented to the outdoors at the top, a check may
be made of the wall between the shaft and the uppermost occupied floor
areas, to ensure that the direction of flow is from each floor area
into the shaft, when the vent to the outside is open and the outdoor
air temperature is significantly less than that indoors. Where mechanically
pressurized vestibules are used, a check may be made to ensure that
the pressure in each vestibule or area of refuge is greater than that
in the adjacent floor areas at each floor level.
Doors to stair shafts, elevator hoistways and vestibules in
locations subject to pressure differences that may interfere with
normal opening should be checked when the outdoor temperature is near
the January design temperature, with the air injection system operating
and a number of windows open to the outdoors on each floor in turn.